How to avoid costly repairs with effective maintenance
In our recent Disrepair Improvement Group session, we heard from Chartered Building Surveyor Geoff Hunt, who shared his extensive knowledge on defect management, planned maintenance, and predictive strategies. With a career that began as a carpenter before transitioning into a foreman and eventually a building surveyor, Geoff brings a unique, hands-on perspective to the challenges of building maintenance.
Defects: understanding context
One of the key points Geoff emphasised was the importance of understanding defects in context. The significance of a defect often depends on perspective. For example, a minor leak in a warehouse may not be urgent, but the same leak over a CEO’s desk during an important interview could cause major disruption. Recognising and prioritising defects based on their impact and setting is crucial for effective maintenance management.
Geoff also highlighted the growing issue of disrepair claims, which can consume a significant number of resources. He stressed the need for organisations to shift from a reactive repairs approach to a planned maintenance strategy. By taking a proactive stance, organisations can not only prevent costly emergency repairs but also enhance efficiency and extend the lifespan of their assets.
Understanding maintenance strategies
Throughout the discussion, Geoff explained the different types of maintenance strategies and their relevance in modern building management. Preventative maintenance involves routine upkeep, such as changing seals, filters, and conducting regulatory inspections. Corrective maintenance, often referred to as reactive maintenance, deals with issues as they arise. Meanwhile, predictive maintenance leverages sensor technology to detect potential failures before they occur, and condition-based maintenance ensures repairs are carried out based on actual wear and tear rather than a predetermined schedule.
The potential of predictive maintenance was a major focus of the session. With advancements in sensor technology, maintenance teams can now monitor equipment performance in real time, allowing them to address issues before they escalate. Geoff encouraged contractors to take the lead in offering predictive maintenance solutions to clients, as these systems not only improve efficiency but also reduce overall maintenance costs.
How standardisation can save time and money
Another significant takeaway from the discussion was the importance of standardisation and smart design. By standardising maintenance components such as door closers, organisations can streamline repairs, reduce costs, and improve response times. Additionally, involving maintenance teams in the design process from the outset can prevent long-term challenges, ultimately saving both time and money.
Beyond these strategic insights, Geoff also provided practical recommendations for seasonal maintenance, including gutter cleaning, tree maintenance, and thermal imaging inspections to identify insulation issues. These proactive measures can help prevent costly damage and improve energy efficiency.
One of the main takeaways from this session was that proactive maintenance is not just about fixing problems as they arise, but about optimising resources, preventing failures, and ensuring the long-term sustainability of buildings. By adopting a planned and predictive maintenance approach, organisations can improve efficiency, reduce costs, and enhance the safety and longevity of their infrastructure.
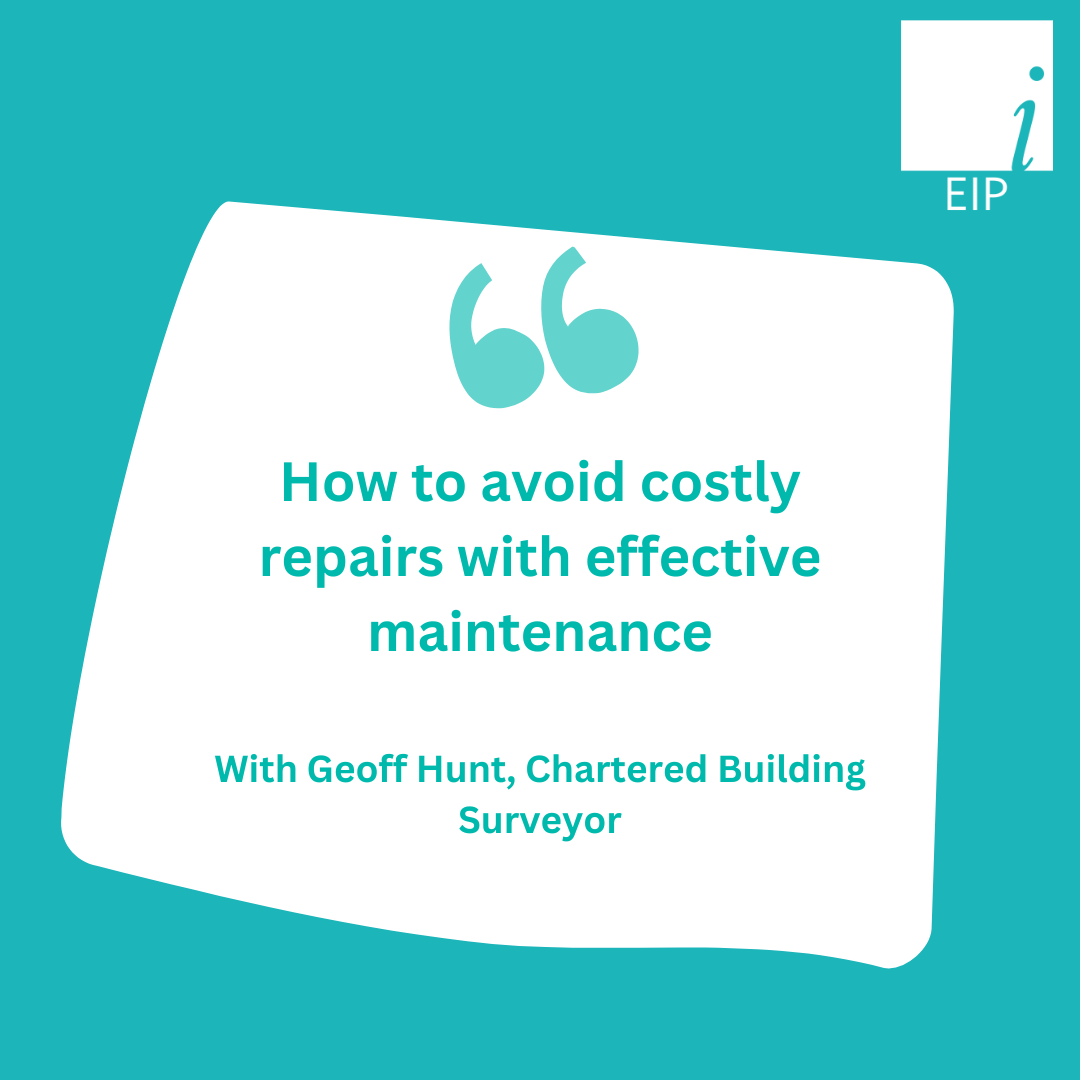